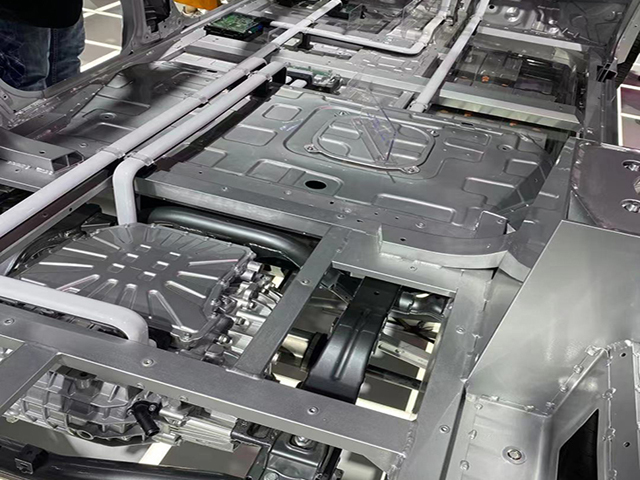
Die Bedeutung von HC950/1300HS
Die Bezeichnung HC950/1300HS bezieht sich auf eine bestimmte Sorte innerhalb der PHS-Familie. Pressgehärtete Stähle (PHS), auch als warmumgeformte oder warmumgeformte Stähle bekannt, sind hochfeste Automobilstahlbleche, die einem einzigartigen Herstellungsprozess unterzogen werden, um ihre gewünschten Eigenschaften zu erreichen.
Die Zahl „950“ stellt die Mindeststreckgrenze in Megapascal (MPa) dar, die der Stahl besitzt, während „1300“ die Mindestzugfestigkeit in MPa darstellt. Diese Werte geben die Fähigkeit des Stahls an, Verformungen zu widerstehen und den aufgebrachten Belastungen standzuhalten.
Das „HS“ steht für „hot-stamped“ und bezieht sich auf das Herstellungsverfahren, mit dem diese Stähle hergestellt werden. Beim Heißprägen wird das Stahlblech auf eine erhöhte Temperatur (typischerweise etwa 900–950 Grad Celsius) erhitzt und dann in einer Matrize schnell umgeformt und abgekühlt. Dieser schnelle Abschreckprozess führt zur Bildung einer vollständig martensitischen Mikrostruktur im gesamten Stahl, die ihm eine hohe Festigkeit und Härte verleiht.
Chemische Zusammensetzung und mechanische Eigenschaften von HC950/1300HS
Chemische Zusammensetzung von HC950/1300HS
C(MAX): 0,20%-0,25%
Mn(MAX): 1,0%-1,4%
Si(MAX): 0,4%
Mechanische Eigenschaften von HC950/1300HS
YS(MPa): 950-1250
TS(MPa): 1300-1700
EL(%) ≥5%
Was sind pressgehärtete Stähle?
Pressgehärtete Stähle (PHS), auch als warmumgeformte oder warmumgeformte Stähle bekannt, sind eine spezielle Art hochfester Automobilbleche. Sie durchlaufen einen speziellen Herstellungsprozess, bei dem der Stahlbarren auf eine erhöhte Temperatur erhitzt, über einen bestimmten Zeitraum auf dieser Temperatur gehalten und anschließend schnell geformt und abgeschreckt wird, um eine martensitische Mikrostruktur zu erzeugen.
Der Prozess beginnt mit dem Erhitzen des Stahlbarrens über seine Austenitisierungstemperatur, typischerweise etwa 900–950 Grad Celsius (1652–1742 Grad Fahrenheit). Diese Temperatur wird über einen bestimmten Zeitraum aufrechterhalten, um die vollständige Umwandlung der Mikrostruktur in Austenit zu ermöglichen.
Sobald der Stahl die gewünschte Temperatur erreicht hat, wird er schnell in ein Formwerkzeug überführt, wo er einer Hochdruckumformung unterzogen wird. Die Matrize formt den Stahl in die gewünschte Endform, beispielsweise für Karosserieteile wie Säulen, Verstärkungen und Seitenaufprallträger.
Unmittelbar nach der Umformung wird der warmumgeformte Stahl durch Abkühlen in der Form unter Verwendung von gekühltem Wasser oder speziellen Kühlmedien schnell abgeschreckt. Durch diesen schnellen Abschreckprozess wandelt sich der Austenit in eine vollständig martensitische Mikrostruktur um, was zu einer hohen Festigkeit und Härte führt.
Die einzigartige Mikrostruktur von PHS, die hauptsächlich aus Martensit besteht, trägt zu seinen außergewöhnlichen Eigenschaften bei. Pressgehärtete Stähle bieten eine Kombination aus hoher Festigkeit, hervorragender Formbarkeit und überlegener Crash-Leistung. Sie sorgen für eine verbesserte Energieabsorption bei einem Aufprall, was die Sicherheit des Fahrzeugs und seiner Insassen erhöht.
PHS wird häufig in Karosseriestrukturteilen von Automobilen eingesetzt, insbesondere in Bereichen, in denen einbruchsichere Sicherheit erforderlich ist. Diese hochfesten Stähle tragen zur Stärkung der Fahrzeugstruktur bei, bieten Widerstand gegen Verformungen bei einem Aufprall und schützen so die Passagiere.
Was sind die Vorteile von HC950/1300HS?
HC950/1300HS, eine spezielle Sorte pressgehärteten Stahls (PHS), bietet mehrere Vorteile für Automobilanwendungen. Hier sind einige seiner wichtigsten Vorteile:
Hohe Festigkeit: HC950/1300HS-Stahl besitzt eine außergewöhnlich hohe Zugfestigkeit. Diese hohe Festigkeit ermöglicht die Herstellung von Leichtbauteilen ohne Beeinträchtigung der strukturellen Integrität oder Unfallsicherheit.
Verbesserte Crashsicherheit: Die martensitische Mikrostruktur, die durch den Warmumform- und Abschreckprozess erzielt wird, verleiht HC950/1300HS eine außergewöhnliche Crash-Performance. Der Stahl ist in der Lage, bei einem Aufprall große Energiemengen zu absorbieren und abzuleiten, was die Sicherheit der Fahrzeuginsassen erhöht.
Leichtbau: HC950/1300HS ermöglicht Leichtbau in Automobilanwendungen. Sein hohes Verhältnis von Festigkeit zu Gewicht ermöglicht eine Reduzierung der Materialstärke und des Gewichts bei gleichzeitiger Wahrung der strukturellen Integrität. Dies trägt zu einer verbesserten Kraftstoffeffizienz und reduzierten Emissionen bei.
Einbruchschutz: Die hohe Festigkeit von HC950/1300HS macht es gut für den Einsatz in einbruchsicheren Sicherheitsbauteilen geeignet. Diese Komponenten tragen dazu bei, den Fahrgastraum bei einem Aufprall zu schützen, indem sie eine übermäßige Verformung und ein Eindringen in den Fahrgastraum verhindern.
Wo wird der HC950/1300HS im Allgemeinen eingesetzt?
HC950/1300HS ist ein hochfester pressgehärteter Stahl (PHS) und wird häufig in verschiedenen Automobilanwendungen verwendet, bei denen überlegene Festigkeit, Unfallsicherheit und Sicherheit von entscheidender Bedeutung sind. Zu den spezifischen Bereichen, in denen der HC950/1300HS typischerweise eingesetzt wird, gehören:
Verstärkungen: HC950/1300HS wird häufig für Verstärkungskomponenten in der Karosseriestruktur von Kraftfahrzeugen eingesetzt. Diese Komponenten verbessern die allgemeine strukturelle Integrität des Fahrzeugs und unterstützen kritische Bereiche wie Säulen, Schweller, Dachreling und Bodenverstärkungen. Durch den Einsatz von HC950/1300HS zur Verstärkung können Hersteller die erforderliche Festigkeit und Steifigkeit der Karosseriestruktur sicherstellen.
Sicherheitselemente: HC950/1300HS wird häufig bei der Herstellung sicherheitsrelevanter Komponenten in Fahrzeugen eingesetzt. Dazu gehören Seitenaufprallschutzträger, Türschutzträger und Stoßfängersysteme. Diese Sicherheitselemente sollen bei einem Aufprall Energie absorbieren und ableiten, die Insassen schützen und das Eindringen der Aufprallkräfte in den Fahrgastraum minimieren.