What is Coiled Tubing?
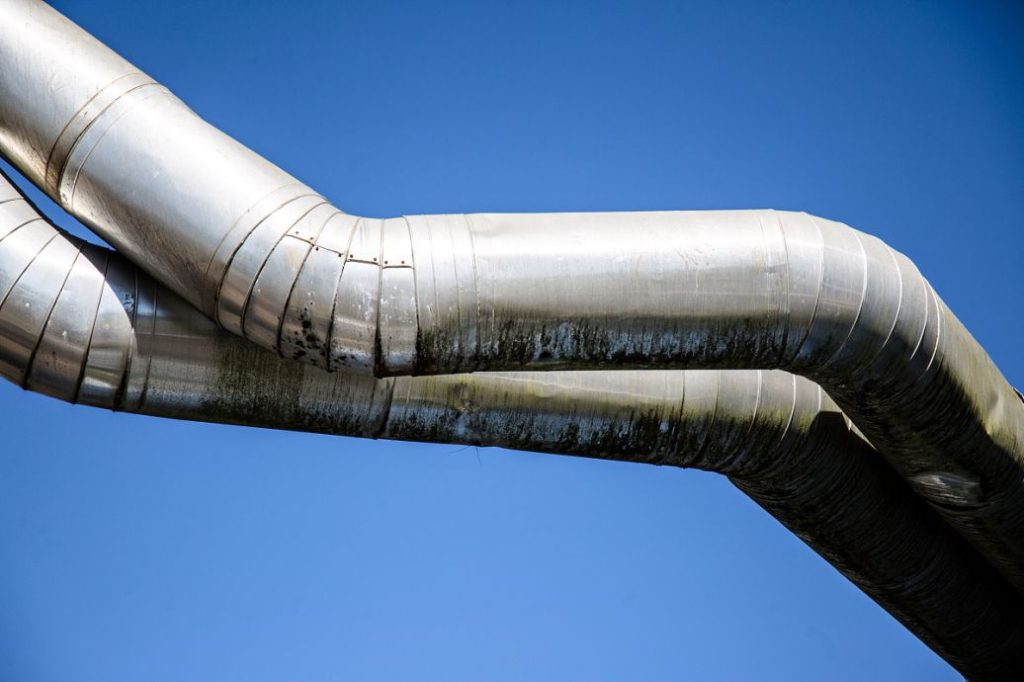
Coiled Tubing (CT for short)
It is a jointless continuous pipe welded by several sections of flexible pipe with a length of more than 100 meters through butt welding or oblique welding. The length is generally several hundred meters to several thousand meters; Also known as flexible tubing, serpentine or coiled tubing.
Coiled tubing is widely used in well workover, well logging, drilling, well completion, as well as well site gathering and transportation pipelines, marine pipelines, etc.
What is the process of coiled tubing operation ?
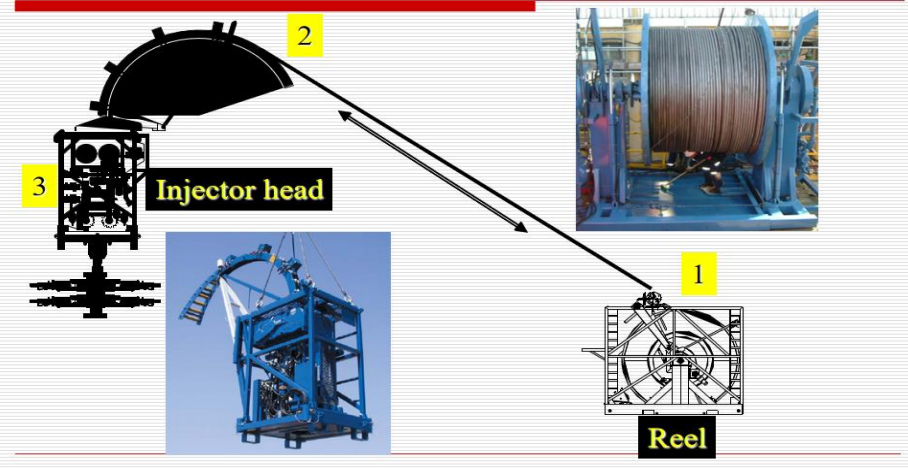
Coiled tubing is a method of operating and maintaining an oil well that allows operations without having to raise the drill pipe or completely shut down the wellhead. The following is the general coiled tubing operation process:
Preparation: First, you need to prepare the required equipment and tools. This may include coiled tubing, hydraulic drive units, tool tandem systems, control lines, and other related tools and accessories.
Installation: Install coiled tubing and related equipment to the wellhead. A special water injector is usually used to introduce the coiled tubing into the well and ensure it is properly positioned and secured.
Connect the mechanical sealing device (packers): according to the operation requirements, install the mechanical sealing device (packers) at the appropriate position in the wellbore. Packers are able to isolate different well formations and prevent fluid leakage.
Hydraulic control: The coiled tubing is controlled by a hydraulic drive unit. The hydraulic control system can realize functions such as expansion, rotation and propulsion of the coiled tubing.
Operation execution: Through coiled tubing, various operations can be carried out, such as workover, repair of fractures, injection of chemical agents, sampling, measurement of pressure and temperature in the well, etc. These operations can be performed according to specific needs.
Completing the job: Once the required jobs have been completed, the coiled tubing equipment can be evacuated and removed from the well.
It should be noted that the specific steps of the coiled tubing operation process may vary due to different operation requirements and geological conditions. Each operation needs to be planned and executed according to the actual situation, and to comply with relevant safety regulations and operating guidelines.
Coiled Tubing Performance Requirements
When the coiled tubing is in use, it is subject to repeated bending deformation, and each time it is pulled up, sent downhole, and used, it will bear 6 times of bending.
When the coiled oil pipe is in service, it is subjected to repeated bending deformation and needs to withstand a large amount of plastic deformation.
Low yield ratio: The lower the yield ratio, the greater the deformation required for the material from the beginning of plastic deformation to fracture, which improves the plastic deformation ability and can effectively relieve the stress concentration caused by overload.
High low-cycle fatigue performance: the stress of coiled tubing reaches the yield point of the material in one cycle, and under the repeated action of this alternating stress (or strain), it is easy to initiate cracks, expand and cause fracture, and the low-cycle fatigue failure way to break.
High corrosion resistance: the life of coiled tubing is also related to corrosion factors.
CT90 Coiled Tubing Steel Performance Index
CT90 means coiled tubing with a minimum yield strength of 80,000 psi in American strength units (80,000 psi is equivalent to 555 MPa). Molten steel and inclusions control purity
The material has high resistance to fatigue cracking, so the purity of the molten steel is required to be high, and the inclusion levels of A, B, C, and D are all required to be no more than 0.5.
Chemical Composition Control
Grade
| CT90 | ||||||||
Chemical composition | C% | Si% | Mn% | Nb% | Ti% | Cu% | Ni% | Cr% | Mo% |
0.04 | 0.24 | 1.38 | 0.11 | 0.012 | 0.24 | 0.15 | 0.58 | 0.33 |
Mo element content increased
√The hardenability of the experimental steel is improved, which is conducive to obtaining the M/A island structure
√It is beneficial to obtain continuous yield type tensile curve
√ As a hard phase in experimental steel to increase its tensile strength
√ A lower yield-to-strength ratio can be obtained
√Mo element promotes acicular ferrite transformation
√It is beneficial to obtain the target organization of acicular ferrite
Nb element content
Fine grain strengthening and precipitation strengthening mainly contribute to the yield strength of the material
In the on-site trial production, the yield strength of the steel plate can reach its performance index
Through the comparison, it can be seen that the influence of Mo and Nb elements on the microstructure and properties of CT90 coiled tubing steel provides a basis for the subsequent on-site production chemical composition adjustment of coiled tubing steel of different grades and specifications.
Mechanical properties index
Yield strength | Tensile strength | Elongation | Yield strength ratio |
≥550MPa | ≥621MPa | ≥24.5% | ≤0.88 |
Process parameter control
Finishing temperature
Cooling rate: control the ferrite form in the finished product structure, and ensure that the acicular ferrite is fully transformed to ensure that the finished product obtains a higher yield strength.
Coiling temperature: Control the morphology of hardening phase in the structure of the finished product, and martensitic transformation occurs at a low temperature to ensure that the finished product obtains qualified strength requirements. Reasonable coiling temperature should be selected to ensure sufficient bainite transformation and avoid pearlite or coiling at excessively high coiling temperature.
On the basis of reasonable chemical composition, by adjusting and controlling the cooling process, that is, adjusting the cooling rate and coiling temperature, a dual-phase structure of acicular ferrite and bainite can be obtained, thereby ensuring the high-strength and low-yield steel for coiled tubing than performance requirements.
key control technology
(1) Optimized design of chemical composition;
(2) Purity steel production and inclusion control technology that meet the quality requirements;
(3) Key technologies for microstructure design and control that meet high-strength, low-yield ratio performance;
(4) Controlled rolling, controlled cooling and non-quenching and tempering production process parameters optimization; mainly including: heating temperature, final rolling temperature, post-rolling cooling speed, deformation amount and deformation rate, etc.;
Application of CT90 Coiled Tubing
Coiled tubing machines are mainly used in the following aspects: sand flushing, drilling bridge plugs, gas lift, liquid nitrogen injection, wax removal, liquid drainage, acid squeezing and coordination testing. Among them, sand washing plugging, gas lift drainage and wax removal are the most common applications, and these three applications account for more than 95% of the total. Coiled tubing operations are gaining popularity in the oilfield.
Advantages of CT90 technology
Compared with ordinary oil well tubing, the advantages of coiled tubing:
◆Without threaded connection, the operation reliability and safety are high;
◆Relocation and installation are fast, greatly improving work efficiency;
◆It can work under pressure without stopping production;
◆The operation site occupies less land, is flexible and convenient
◆The operation cost is greatly reduced, which can save 50%-70% of the cost.
Development Status of Coiled Tubing
● Coiled tubing technology has been rapidly developed and widely used in North America and developed regions. By 2010, there were more than 1,778 CTUs in the world, and 49 in China.
● In North America, coiled tubing is the most widely used, accounting for more than 60% of the world’s annual consumption, with an annual growth rate of 10%-15%.
Rapid development and wide application in foreign countries; slow domestic development, but a large market space, with the development of coiled tubing technology, the demand for steel for domestic coiled tubing is bound to increase gradually.
Development trend of coiled tubing and its steel
High Strength Coiled Tubing | ||||
Grade | Yield Strength, MPa | Tensile Strength, MPa | Elongation, % | Hardness, HRC |
CT55 | ≥379 | ≥483 | ≥30 | ≤22 |
CT70 | ≥483 | ≥552 | ≥30 | ≤22 |
CT80 | ≥551 | ≥621 | ≥27 | ≤22 |
CT90 | ≥620 | ≥669 | ≥22 | ≤22 |
CT100 | ≥689 | ≥758 | ≥22 | ≤28 |
CT110 | ≥758 | ≥793 | ≥20 | ≤30 |
Baosteel Coiled Tubing Steel Situation
At present, three grades of high-strength coiled tubing steel, CT80, CT90, and CT100, have been developed and exported to overseas in batches, but they are not completely supplied to domestic steel pipe manufacturers.
Chemical Composition of Baosteel CT90 Coiled Tubing Steel
C | Si | Mn | Nb | Ti | Cu | Ni | Cr | Mo | |
Min | 0.04 | 0.24 | 1.38 | 0.11 | 0.012 | 0.24 | 0.15 | 0.58 | 0.33 |
Max | 0.05 | 0.56 | 1.13 | 0.09 | 0.015 | 0.45 | 0.25 | 0.63 | 0.16 |
Baosteel CT90 Coiled Tubing Steel Process Parameters
Finishing temperature, ℃ | Cooling rate, ℃/s | Coiling temperature, ℃ | |
1# | 800 | 8–14 | 450-500 |
2# | 840 | 12–18 | 500-550 |
Mechanical properties of Baosteel CT90 steel for coiled tubing
Yield strength, MPa | Tensile strength, MPa | Elongation, % | |
1# | 650 | 710 | 23.4 |
2# | 625 | 681 | 25 |
WISCO Coiled Tubing Steel Situation
◆WISCO began to develop steel for coiled tubing in 2006, and successively carried out 6 or 7 rounds of on-site trial production, each round of smelting in two furnaces, and it was not successfully developed until the end of 2009;
◆ CT70 and CT80 grades of steel for coiled tubing can be produced stably;
◆ Steel specifications for CT80 coiled tubing supplied by WISCO are all below 4mm, and the diameter specifications of coiled tubing produced are mostly below φ31.75mm;
◆At present, CT90 steel for coiled tubing is being developed.
Shangang CT90 pipeline steel
In order to better meet customer needs, Shandong Iron and Steel Group Rizhao Co., Ltd. responded quickly, and the Science and Technology Quality Center led the production unit to form a team to promote product development. The team members actively collaborated to break through a series of control problems such as product composition, performance, plate shape and surface through the adoption of innovative metallurgical schemes and process technologies, and successfully trial-produced high-strength coiled tubing steel CT90 in a short period of time. After inspection, the product composition is qualified, the mechanical properties are stable, the shape and surface quality are good, and all indicators meet the requirements of the user’s technical agreement. The first batch of orders has been sent to households one after another.