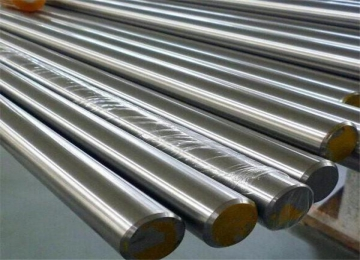
TC11 titanium alloy is an α-β type heat-strength titanium alloy with good comprehensive properties. It has excellent heat-strength properties and room temperature strength, as well as good hot processing processability and machining performance. The alloy is mainly used to manufacture parts such as compressor disks, blades, and drums of aeroengines, as well as aircraft structural parts. Through thermal deformation in the α+β zone and heat treatment in the α+β zone, the maximum long-term operating temperature of TC11 alloy can be obtained at 500°C. The semi-finished products produced include bars, forgings, die forgings and castings, etc. In short, TC11 titanium alloy is a very important material with broad application prospects.
TC11 chemical element composition content (%)
Lorem ipsum dolor sit amet, consectetur adipiscing elit. Ut elit tellus, luctus nec ullamcorper mattis, pulvinar dapibus leo.
TC11 heat treatment system
The heat treatment system of TC11 titanium alloy mainly includes double annealing and stress relief annealing.
The specific system of double annealing is: first perform high-temperature annealing at a temperature of 950°C, holding time for 1-2 hours, and then air cooling; then perform low-temperature annealing at a temperature of 530°C, holding time for 6 hours, and then air cooling again. It should be noted that the first annealing temperature can be appropriately adjusted within the range of 30-50°C below the β phase transition point, while the first annealing holding time is determined based on the maximum section thickness, 1 hour for 25mm and below, and 1.5 hours for 26-50mm. , 51-75mm is 2 hours.
The specific system of stress relief annealing is: the temperature range is 530-580°C, the holding time is 0.5-6 hours, and then air cooling or furnace cooling is performed.
In short, these heat treatment systems can effectively improve the performance and service life of TC11 titanium alloy, making it more suitable for use in high-temperature and high-pressure environments such as aerospace engines.
TC11 smelting and casting process
The smelting process of TC11 titanium alloy requires more than two vacuum consumable electrode arc furnace smelting.
Specifically, the smelting process of TC11 titanium alloy requires the use of a vacuum consumable electrode arc furnace. This furnace can be smelted in a vacuum environment to avoid oxidation and pollution. During the smelting process, the alloy needs to be smelted more than twice to ensure the purity and uniformity of the alloy.
After smelting is completed, it can be processed using a variety of casting techniques, such as sand casting, pneumatic mold casting, isostatic casting, etc. These casting processes can be selected based on specific application needs and processing requirements to obtain the best processing results and performance.
In short, the smelting and casting process of TC11 titanium alloy needs to be strictly controlled to ensure the quality and performance of the alloy.
TC11 welding performance
TC11 titanium alloy can be used in welded structures, but it must be protected by inert gas (argon, helium) or vacuum methods during welding to avoid oxidation. The weld should have no oxidation or yellowish color.
Since this alloy reacts greatly to the thermal cycle of welding, some specialized heat treatment methods are required to eliminate residual stress and stabilize the structural properties of the weld and the metal in the adjacent area of the weld. It is generally recommended to anneal after welding and perform air cooling or furnace cooling. Annealing should be performed in a vacuum furnace or inert gas container. The use of flame spray guns for annealing is not allowed.
In short, the welding performance of TC11 titanium alloy is better, but appropriate welding methods and heat treatment methods need to be used to ensure welding quality and material properties.
TC11 Application Overview
TC11 titanium alloy is a high-strength, high-temperature alloy that is mainly used to manufacture parts such as compressor disks, blades, and drums of aeroengines, as well as aircraft structural parts.
Because TC11 titanium alloy has excellent high-temperature strength and thermal stability, it can work in high-temperature environments for a long time. Based on the information you provided, the allowed working time of this alloy is 6000 hours at 450°C and 500 hours at 500°C. These data show that TC11 titanium alloy can work in high temperature environments for a long time and has good high temperature stability.
In addition to aero engines and aircraft structural parts, TC11 titanium alloy can also be used to manufacture parts in other high-temperature working environments, such as steam turbine blades, chemical equipment, etc. In short, TC11 titanium alloy is an important high-strength and high-temperature alloy with broad application prospects in aviation, energy, chemical industry and other fields.