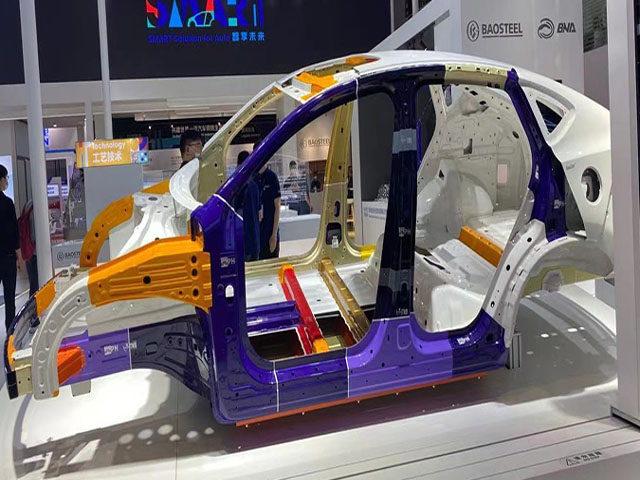
The meaning of HC700/900MS
The “HC” in HC700/900MS stands for “High Strength Cold Rolled”. The number “700” represents the minimum yield strength in megapascals (MPa) that the steel possesses, while “900” represents the minimum tensile strength in MPa. These values indicate the steel’s ability to resist deformation and withstand applied loads.
The “MS” in HC700/900MS stands for “Martensitic Steel”.Martensitic steel (MS) refers to a type of steel that exhibits a specific microstructure known as martensite. Martensite is a hard, brittle phase that forms in steel when it undergoes a rapid cooling or quenching process from a high temperature. This transformation gives martensitic steels their distinctive properties, such as high strength, hardness, and wear resistance.
Chemical composition and mechanical properties of HC700/900MS
Chemical composition of HC700/900MS
C(MAX): 0.2%
Mn(MAX): 2%
Si(MAX): 0.6%
Mechanical properties of HC700/900MS
YS(MPa): 700-900
TS(MPa): ≥900
EL(%) ≥4%
What is Martensitic Steel?
Martensitic steel is a type of steel that exhibits a significant amount of martensite structure, which is responsible for its exceptional strength. The formation of this structure is achieved through a process involving cold rolling and continuous annealing, followed by quenching.
Cold rolling is a manufacturing process that involves reducing the thickness of a metal sheet or strip by passing it through a series of rollers at ambient temperature. This process not only reduces the material’s thickness but also increases its strength and hardness due to plastic deformation. Cold rolling also imparts a preferred orientation to the crystalline structure of the steel, enhancing its mechanical properties.
After cold rolling, the steel undergoes continuous annealing, also known as continuous heat treatment. This process involves heating the steel to a specific temperature range and holding it there for a certain period, followed by controlled cooling. Continuous annealing helps to relieve the internal stresses induced by cold rolling, refine the microstructure, and improve the material’s formability.
Once the continuous annealing process is complete, the steel is rapidly quenched. Quenching involves cooling the material rapidly to room temperature or below, typically using a liquid medium such as water or oil. This rapid cooling prevents the formation of other crystal structures, such as ferrite or pearlite, and promotes the formation of martensite.
Martensite is a highly desirable microstructure in terms of strength, as it consists of lath-shaped crystals with a fine and needle-like structure. This unique arrangement provides the steel with excellent hardness, tensile strength, and wear resistance. Martensitic steels are known for their ability to withstand high mechanical stresses and exhibit good dimensional stability.
What are the advantages of HC700/900MS?
Here are some of the key advantages of HC700/900MS:
High Strength: HC700/900MS steel has a minimum yield strength of 700 MPa and a minimum tensile strength of 900 MPa. This high strength allows the steel to withstand heavy loads and resist deformation, making it suitable for applications where strength is a critical factor.
Hardness and Wear Resistance: Martensitic steels, including HC700/900MS, are known for their exceptional hardness. The martensite microstructure present in HC700/900MS steel contributes to its hardness, which makes it highly resistant to wear and abrasion. This property is advantageous in applications where the steel is subjected to abrasive conditions or needs to maintain its shape under high stresses.
Dimensional Stability: HC700/900MS steel exhibits good dimensional stability, meaning it retains its shape and size even under significant mechanical stresses or changes in temperature. This makes it suitable for applications where maintaining precise dimensions is essential, such as in structural components or parts subject to heavy loads.
Application of HC700/900MS in Automobile Field
HC700/900MS steel finds various applications in the automobile field due to its desirable properties. Here are some common applications of HC700/900MS in the automotive industry:
Structural Components: HC700/900MS steel is often used for manufacturing structural components in automobiles that require high strength and excellent dimensional stability. It can be employed in chassis frames, body-in-white structures, reinforcements, and safety-critical components such as door beams and bumper reinforcements. The high strength of HC700/900MS ensures enhanced crashworthiness and structural integrity, contributing to improved safety.
Suspension Systems: The high strength and hardness of HC700/900MS make it suitable for suspension components such as coil springs, stabilizer bars, and torsion bars. These components need to withstand significant mechanical stresses, and the high strength of HC700/900MS ensures durability and longevity.
Exhaust Systems: HC700/900MS can be utilized in exhaust systems, particularly in areas where high-temperature resistance and corrosion resistance are required. The martensitic structure of the steel provides the necessary strength and hardness, enabling the exhaust system components to endure harsh operating conditions.
Reinforcements and Brackets: HC700/900MS steel can be used for reinforcements and brackets in various areas of the vehicle, including the engine compartment and underbody. These components require high strength and stiffness to provide structural support and to withstand the loads and vibrations encountered during vehicle operation.
Door Intrusion Beams: HC700/900MS steel can be employed in the manufacturing of door intrusion beams, which are designed to enhance occupant protection in the event of a side impact. The high strength and toughness of HC700/900MS help absorb and distribute impact energy, minimizing the intrusion into the passenger compartment.