Zinc Aluminum Magnesium Steel
Zinc Aluminum Magnesium Steel coil is a new type of high corrosion resistance coated steel plate. Its coating composition is mainly zinc, which is composed of zinc plus 1.5% – 11% aluminum, 1.5% – 3% magnesium and trace silicon (the proportion of different manufacturers is slightly different). At present, the thickness of Zinc Aluminum Magnesium Steel range that can be produced in China is 0.4-4.0mm, and the width range that can be produced is 580mm-1500mm.
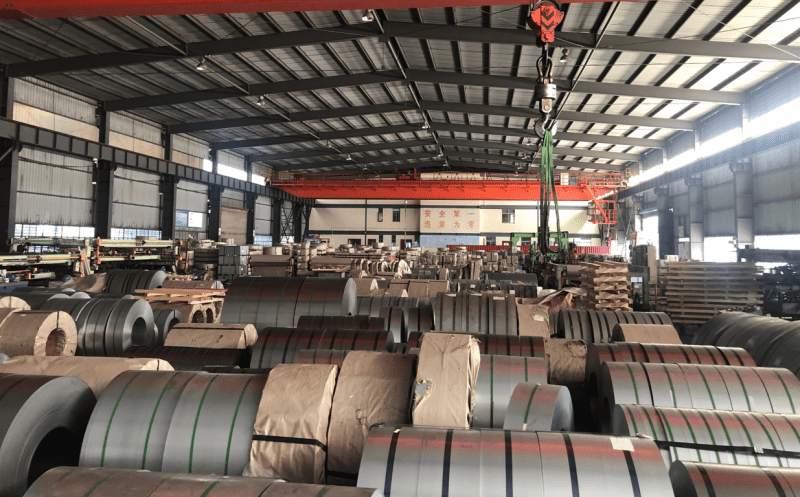
Zinc Aluminum Magnesium Steel Coils Factory
Due to the compound effect of these added chemical elements, the corrosion inhibition effect is further improved. In addition, Zinc Aluminum Magnesium Steel has excellent processing performance under severe conditions (tensile stamping, bending, paint welding, etc.), high coating hardness and excellent damage resistance. Compared with ordinary zinc plating or stainless steel, this kind of product has superior corrosion resistance and corrosion resistance. The corrosion resistance and self-healing effect of the cutting end face is a major feature of the product.
Advantage of Zinc Aluminum Magnesium Steel
1. Plane corrosion resistance
High aluminum zinc aluminum magnesium coating, has significantly better plane corrosion resistance than aluminum zinc coating, and hot-dip pure zinc coating. Under the condition of neutral salt spray test, the time of red rust in high aluminum zinc aluminum magnesium coating, is more than 50% longer than that of aluminum zinc coating with the same thickness. Under the condition of cyclic corrosion test, the time of red rust in high aluminum zinc aluminum magnesium coating is nearly twice longer than that of GL coating with the same coating thickness.
2. Corrosion resistance
Notch corrosion resistance the notch corrosion resistance of high aluminum zinc aluminum magnesium coating, is significantly better than that of aluminum zinc coating. Under the condition of neutral salt spray test, the greater the zinc ratio index is, compared with that of aluminum zinc coating, as is the greater the notch corrosion resistance of high aluminum zinc aluminum magnesium coating.
3. Cup punching corrosion resistance
Under the condition of neutral salt spray test, the red rust time of high aluminum zinc aluminum magnesium coating, is about twice as long as that of aluminum zinc coating.
4. Bending corrosion resistance
Under the condition of neutral salt spray test, the corrosion resistance of high aluminum zinc aluminum magnesium coating after bending is about twice higher than that of aluminum zinc coating.
The Application of Zinc Aluminum Magnesium Steel
Zinc aluminum magnesium steel products are widely used in civil construction (keel ceiling, perforated plate, cable bridge), agricultural livestock products (agricultural breeding shed, steel structure, steel structural accessories, greenhouse, breeding equipment), railway roads, power communication (transmission and distribution high and low voltage switchgear, box type substation outer body), photovoltaic support, automobile motor, industrial refrigeration (cooling tower, large outdoor industrial air conditioning) and other industries.
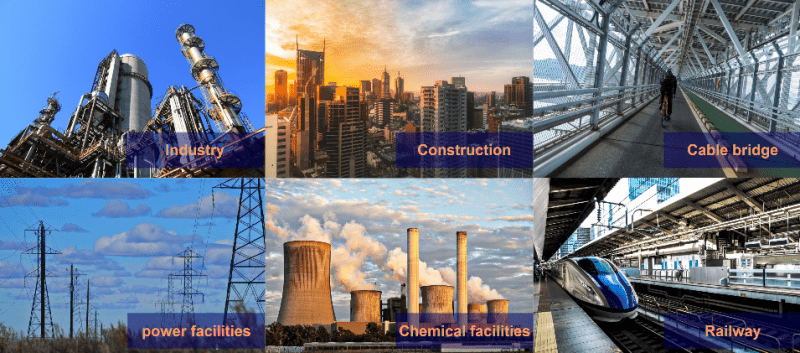
Zinc Aluminum Magnesium Steel Application
Order Attention about Zinc Aluminum Magnesium Steel
Zinc aluminum magnesium steel products have a wide range of industry usages. For different purposes, different ordering standards are configured, such as: ① passivation + oiling, ② non passivation + oiling, ③ passivation + non oiling, ④ non passivation + non oiling, ⑤ fingerprint resistance. Therefore, in the process of small batch procurement and use, it is necessary to confirm the use scenario and surface delivery requirements, as with the supplier to avoid subsequent processing problems.
Zinc Aluminum Magnesium Steel Prices
The price of Zinc Aluminum Magnesium steel is mainly determined by steel coil weight, packaging mode, transportation distance and delivery way and other factors.
1. how to measure the weight of Zinc Aluminum Magnesium steel plate or coil?
The nominal weight of the coils is as weighted. For the asrolled coils, the weight range differs according to the lines.
The available weight increases when the width increases. The available weight is listed as following:
steel coils price: parameter*width*Unit Price
steel sheet/plate price: width*length*thickness*parameter*number of sheets *Unit Price
2. packaging mode
The different packaging mode will affect the final price. if you are not sure about the packaging mode, we can give you the professional advice.
3.transportation distance and delivery way
So-Lucky can provide you the variety delivery way. For instance, train, plane, ship or automobile. The delivery time is also important for you. If you ensure the transportation distance and delivery way of Zinc Aluminum Magnesium steel.
If you are interested with our Zinc Aluminum Magnesium steel coil or sheet/plate, you can contact us to get more Zinc Aluminum Magnesium steel products price here. we will answer you as soon as possible.
Zinc Aluminum Steel FAQS
What is zinc aluminum steel?
zinc aluminum steel is an alloy-coated steel sheet widely used in building materials, home appliances, automobiles, environment, machinery, ships and many other fields.
zinc aluminum steel is composed of aluminum-zinc alloy structure, which is composed of 55% aluminum, 43.4% zinc and 1.6% silicon solidified at a high temperature of 600°C. The entire structure is composed of aluminum-iron-silicon-zinc, forming a dense quaternary crystal An alloy coated steel plate.
What are the characteristics of zinc aluminum steel?
zinc aluminum steelhas many excellent characteristics:
Corrosion resistance:
The corrosion resistance of “galvanized steel coil” is mainly due to the protective function of aluminum. When the zinc is worn away, the aluminum forms a dense layer of aluminum oxide, which prevents the corrosion-resistant substances from further corroding the interior.
Heat resistance:
The aluminum-zinc alloy steel plate has good heat resistance and can withstand high temperatures of more than 300 degrees Celsius. It is very similar to the high-temperature oxidation resistance of the aluminized steel plate. It is often used in chimney pipes, ovens, illuminators and fluorescent lamp shades.
Heat reflectivity:
The heat reflectance of galvanized steel sheet is very high, which is twice that of galvanized steel sheet. People often use it as heat insulation material.
Economical:
Because the density of 55% AL-Zn is smaller than that of Zn, the area of galvanized steel sheet is more than 3% larger than that of galvanized steel sheet when the weight is the same and the thickness of the gold plating layer is the same.
What are the applications of zinc aluminum steel?
Construction: roofs, walls, garages, sound insulation walls, pipes and prefabricated houses, etc.
Automobile: mufflers, exhaust pipes, wiper accessories, fuel tanks, truck boxes, etc.
Household appliances: refrigerator back panel, gas stove, air conditioner, electronic microwave oven, LCD frame, CRT explosion-proof belt, LED backlight, electrical cabinet, etc.
Agricultural use: pig house, chicken house, granary, greenhouse pipes, etc. Others: heat insulation cover, heat exchanger, dryer, water heater, etc.
What are the uses of zinc aluminum steel?
Storage: It should be stored indoors such as warehouses, kept dry and ventilated, and not placed in acidic climate for a long time. When storing outdoors, it should be protected from rain to avoid oxidative stains caused by condensation. Transportation: To avoid external impact, SKID should be used to support steel coils on the transportation vehicle, to reduce stacking, and to take rainproof measures. Processing: COILCENTER needs to use the same lubricating oil as the aluminum plate when shearing. When it is necessary to drill holes or cut galvanized steel sheets, it is necessary to remove scattered iron filings in time.
What are the differences between zinc aluminum steel and galvanized sheet?
The difference between the zinc aluminum steel and the galvanized sheet is mainly the difference in the coating. The surface of the zinc aluminum steel is evenly distributed with a layer of zinc material, which acts as an anodic protection for the base metal, that is, an alternative corrosion protection for the zinc material. Without the use of the base metal, only when the zinc is completely corroded can the base metal inside be damaged.
The surface coating of the zinc aluminum steel is composed of 55% aluminum, 43.5% zinc and a small amount of other elements. Microscopically, the surface of the galvanized coating is a honeycomb structure, and the “honeycomb” composed of aluminum contains zinc. In this case, although the aluminum-zinc coating also plays the role of anodic protection, on the one hand, due to the reduction of zinc content, on the other hand, the effect of anodic protection is greatly reduced because the zinc material is wrapped in aluminum and is not easy to be electrolyzed. The zinc aluminum steel is cut, and it will rust soon when the cut edge basically loses its protection. Therefore, the galvanized sheet should be cut as little as possible. Once cut, the edge should be protected with anti-rust paint or zinc-rich paint to make it The service life of the panels is extended.
What is the processing process of galvanized sheet?
first step:
Pre-treatment: After the cold-rolled coil comes to the galvanizing workshop, it passes through the uncoiler, the degreasing section and the reduction furnace to clean the steel coil and restore its components to the extent that it can be galvanized.
Step two:
Central section: The most critical technology is this step. After passing through the zinc pot, a layer of zinc is coated on the surface of the steel plate. It will look beautiful immediately after coming out of the zinc pot, and then it will be cooled and shaped by the cooling tower.
third step:
Post-processing: After various processes, the steel plate finally reaches the post-processing stage. After finishing, straightening, and passivation, the steel plate is finally rolled onto the winder to form our final product.
The corrosion resistance of 55% galvanized sheet is 2 to 6 times that of galvanized sheet. Because of its superior corrosion resistance and processing performance, it can be directly used as building roof panels, civil and home appliance back panels, etc., and is also widely used For color coated substrates. The smooth commissioning of galvanized sheet not only enriches the company’s product categories, but also provides more flexible options for future market layout and strategic planning.
What are the advantages of zinc aluminum steel?
The 55%zinc aluminum steel has the protective function of barrier layer from aluminum and the sacrificial protective function of zinc. When zinc is cut and scratched, aluminum will form an insoluble oxide layer to play a protective role. In addition, the density of galvanizing is low, and the coating thickness of the same weight is much thicker than that of galvanizing. In addition to corrosion resistance and high temperature resistance, the 55%zinc aluminum steel has good reflectivity, and the paint coating has good adhesion. There are also 55% galvanized sheets with a variety of spangles, the surface of which is beautiful, and suitable for external use.
What is zinc aluminum magnesium coated steel?
Zinc aluminum magnesium coated steel is a new type of corrosion-resistant steel. It is made by hot-dip coating a layer of aluminum-zinc alloy on the surface of cold-rolled steel sheet. The alloy layer consists of 55% aluminum, 43.4% zinc and 1.6% magnesium. The coating has good corrosion resistance, heat resistance and electrochemical properties, and can be used in a wide range of applications.
What are the benefits of using zinc aluminum magnesium coated steel?
Zinc aluminum magnesium coated steel is a new type of steel that has been coated with a zinc-aluminum-magnesium alloy. This Alloy provides an excellent corrosion resistance to both galvanic and atmospheric corrosion. The key benefits of using this type of steel are as follows:
1) An excellent corrosion resistance – The alloy coating on zinc aluminum magnesium coated steel provides an outstanding barrier against corrosion in both industrial and marine environments.
2) A long service life – The exceptional protection offered by the zinc aluminum magnesium coating ensures that the underlying steel will enjoy a long service life, even in the most challenging environments.
3) Aesthetics – The attractive silver-gray finish of zinc aluminum magnesium coated steel is both pleasing to the eye and easy to maintain.
- Environmentally friendly – The zinc aluminum magnesium coating is completely recyclable, making this an environmentally friendly option for your next building project.
What are the advantages of Zinc Aluminum Magnesium Coated Steel?
Zinc aluminum magnesium coated steel is a new type of highly corrosion-resistant coated steel. Zinc, aluminum and magnesium all have excellent corrosion resistance properties, so this new type of steel should theoretically be even more resistant to corrosion than traditional galvanized steel.
One of the key advantages of zinc aluminum magnesium coated steel is that it can be used in environments where traditional galvanized steel would typically not perform well. This includes highly corrosive environments such as coastal areas or areas with high levels of pollution.
Another advantage of this type of steel is that it offers increased protection against UV light. This means that it can be used in outdoor applications without fear of the coating deteriorating over time.
Overall, zinc aluminum magnesium coated steel offers superior corrosion resistance and durability compared to traditional galvanized steel, making it an ideal choice for a wide range of applications.
What are the Disadvantages of Zinc Aluminum Magnesium Coated Steel?
Zinc aluminum magnesium coated steel is a type of galvanized steel that has been treated with an alloy of zinc, aluminum, and magnesium. This coating is applied to create a barrier against corrosion and rust. The advantages of this process include a longer lifespan for the steel and greater protection against the elements. However, there are also some disadvantages to consider before using this material.
One potential disadvantage of zinc aluminum magnesium coated steel is that it may be more expensive than other types of galvanized steel. This is because the process of applying the coating is more complex and requires specialized equipment. Additionally, the materials used in the coating are typically more expensive than those used in other methods of galvanization.
Another downside to this type of steel is that it can be more difficult to work with. The coating can make the surface of the metal harder to cut, weld, or bend. This can make it challenging to fabricate parts or constructions from this material. As a result, it is important to consult with experts before attempting to use zinc aluminum magnesium coated steel in any project.
What is the process of Zinc Aluminum Magnesium Coating Steel?
The process of zinc aluminum magnesium coating steel is a multi-step process that begins with the cleaning of the steel. The steel is then dipped in a hot-dip galvanizing bath, which provides the zinc aluminum magnesium coating.
How is zinc aluminum magnesium coated steel heat treated?
Zinc aluminum magnesium coated steel is heat treated by first being passed through a hot-dip process, in which the steel is dipped into a bath of molten zinc. This gives the steel a thin layer of zinc on its surface. The steel is then cooled and passed through an annealing process, which helps to improve its ductility. Finally, the steel is passed through a hot-dip galvanizing process, in which it is coated with a layer of zinc and aluminum.
Are there any common products that use zinc aluminum magnesium coated steel?
Magnesium is the primary element in this coating and it provides many benefits. For instance, it increases the corrosion resistance of the steel. Zinc and aluminum are also important elements in this type of steel coating. Together, they provide a better overall barrier against corrosion than either metal alone.
This type of steel is often used in the production of automobiles, appliances, and construction materials. It is also commonly used in the food and beverage industry due to its high resistance to corrosion.
How to use zinc aluminum magnesium coated steel?
When it comes to using zinc aluminum magnesium coated steel, there are a few things to keep in mind. First, this type of steel is best used for projects that require a high level of corrosion resistance. This means that it is ideal for outdoor use or for areas that are exposed to harsh chemicals. Second, because this type of steel is so corrosion-resistant, it is also very difficult to weld. This means that you will need to take extra care when welding zinc aluminum magnesium coated steel to ensure a strong and secure bond.
What are the tips for using zinc aluminum magnesium coated steel?
- When welding, use low heat and a short arc.2. Keep the area well ventilated to avoid fumes.
3. Use gloves and a face mask to protect yourself from fumes and sparks.
4. Follow all safety precautions when using power tools.