Introduction
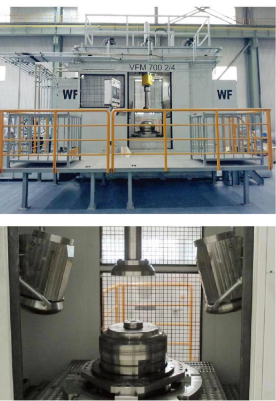
Spinning is a metal forming process that involves spinning a metal blank around a central axis while a tool called a mandrel is pressed against the blank to form it into the desired shape.
Spinning, also known as spin forming or metal spinning, is a metal forming process that has been used for centuries to produce symmetrical, high-precision metal parts. The process involves placing a metal blank on a rotating mandrel and pressing it against the mandrel using a tool called a roller or spinning tool. The metal is then formed into the desired shape by the action of the tool, while the mandrel provides support for the inner surface of the formed part.
Advantage
Spinning offers several advantages over other metal forming methods such as casting, stamping and machining. These advantages include:
High precision: Spin forming can produce high-precision parts with tight tolerances, suitable for industries such as aerospace and medical.
Versatility: Spin forming can be used to produce a variety of shapes and sizes, including cylindrical, conical and spherical.
Cost-effective: Spin forming can produce parts quickly and with minimal waste, reducing production costs.
Improve material properties: Spin forming can improve the strength and fatigue resistance of materials by controlling grain structure and reducing material thickness.
Complex shapes: Spin forming can produce complex shapes that would be difficult or impossible to produce using other metal forming methods.
application
Spinning has a wide range of applications in various industries such as aerospace, automotive, medical, lighting, etc. Some examples of rotating parts include:
Aerospace components: Spin forming is used to produce a variety of aerospace components such as engine casings, rocket nozzles and satellite components.
Automotive components: Spin forming is used to produce a variety of automotive components such as wheels, exhaust systems, and fuel tanks.
Medical Devices: Spin forming is used to produce a variety of medical devices such as surgical instruments, prosthetics and medical implants.
Lighting fixtures: Spin forming is used to produce various lighting fixtures, such as lamp shades and reflectors
Application
Spinning has a wide range of applications in various industries such as aerospace, automotive, medical, lighting, etc. Some examples of rotating parts include:
Aerospace components: Spin forming is used to produce a variety of aerospace components such as engine casings, rocket nozzles and satellite components.
Automotive components: Spin forming is used to produce a variety of automotive components such as wheels, exhaust systems, and fuel tanks.
Medical Devices: Spin forming is used to produce a variety of medical devices such as surgical instruments, prosthetics and medical implants.
Lighting fixtures: Spin forming is used to produce various lighting fixtures, such as lamp shades and reflectors.
Product
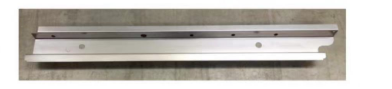
RockerHC950/1180MS, 1.4mm
High Strength Low Alloy Steel (HSLA)
SAE J2340 340X S355MC OStE340TM,
QStE380TM B380CL B420CL B450CL B500CL
B550CLB600CLB650CL
Hot Rolled Dual Phase Steel Hot Rolled Dual Phase Steel
BR330/580DP BR450/780DP
Special steel Special Steel
SAE1050, 26MnB5
High Hole-expansion Steel
BR300/450HEBR440/580HE
BR600/780HE
Spinning is a versatile and cost-effective metal forming process that offers several advantages over traditional metal forming methods, including high precision, versatility, cost-effectiveness, improved material properties, and the ability to produce complex shapes . Its application in various industries continues to grow as more and more companies seek to produce high-quality metal components with minimal waste and production time.
Conclusion
Spinning is a common metalworking process that applies rotation and pressure to a metal material to gradually deform it into the desired shape. This process is mainly used in the manufacture of cylindrical and conical components such as tubes, bearings, gears, etc.
Spinning first appeared in ancient Rome, when people used this method to make various metal utensils and weapons. However, it wasn’t until the late 19th century that the craft became widely used. Nowadays, spinning forming has become one of the important metal processing methods, and it is widely used in aviation, automobile, machinery manufacturing and other fields.
The principle of spinning forming is relatively simple. It only needs to place the metal material in the spinning machine, and then gradually deform it by rotating the mold and applying pressure. Typically, a spinning machine consists of three parts: tip, indenter and die. Tips and indenters are usually made of carbide or high-speed steel in order to be able to withstand high-intensity pressure. The mold is manufactured according to the required shape and consists of multiple sections, which can be combined as required.
Spin forming has many advantages. First, it can produce high-precision parts, especially in the manufacture of small diameter and thin-walled parts. Second, since metal cutting is not required during the spinning process, raw materials are saved and waste is reduced. Finally, spin forming is more productive and has lower production costs than other processing methods.
However, spin forming also has some limitations and disadvantages. First, the process is only suitable for making cylindrical and tapered parts, not other shapes. Second, since metal is deformed by pressure, it is susceptible to external forces such as impact or vibration. Finally, since spin forming requires custom tooling, it can be costly for low-volume production.
In general, spinning forming is an important metal processing technology with broad application prospects. In the future, with the continuous development and improvement of technology, it is believed that the application of spinning forming will become more and more extensive to meet the growing market demand.