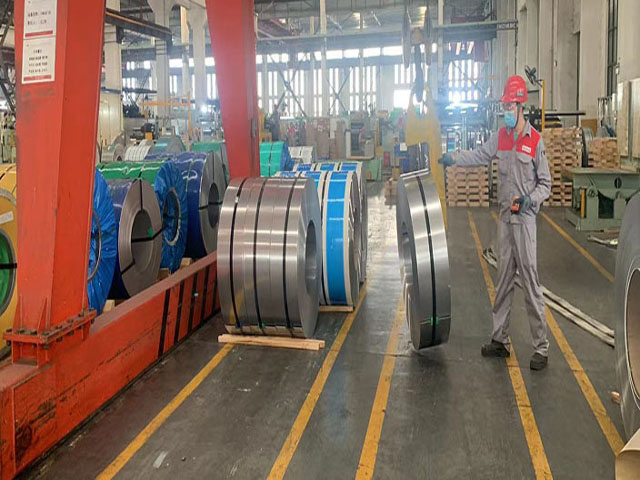
The difference between 304 and 304L stainless steel in chemical composition
The main difference between 304 and 304L stainless steel lies in their carbon content.
The chemical composition of 304 stainless steel typically includes:
Iron (Fe): Balancing element
Chromium (Cr): 18-20%
Nickel (Ni): 8-10.5%
Manganese (Mn): 2%
Silicon (Si): 0.75%
Carbon (C): 0.08% maximum
Phosphorus (P): 0.045% maximum
Sulfur (S): 0.03% maximum
304L stainless steel has a slightly lower carbon content than 304 stainless steel, which results in improved weldability and reduced susceptibility to sensitization during welding. The chemical composition of 304L stainless steel typically includes:
Iron (Fe): Balancing element
Chromium (Cr): 18-20%
Nickel (Ni): 8-12%
Manganese (Mn): 2%
Silicon (Si): 0.75%
Carbon (C): 0.03% maximum
Phosphorus (P): 0.045% maximum
Sulfur (S): 0.03% maximum
This slight variation improves the weldability and corrosion resistance of 304L, making it suitable for specific applications where welding is involved or enhanced corrosion resistance is desired.
What are the key properties difference between stainless steel 304 and 304L?
The key properties difference between stainless steel 304 and 304L primarily arise from the lower carbon content in 304L. Here are the key properties to consider:
Weldability: The lower carbon content in 304L stainless steel provides improved weldability compared to 304 stainless steel. The reduced carbon content helps to minimize the formation of chromium carbide precipitates at the grain boundaries during welding, which can cause sensitization and subsequent intergranular corrosion.
Corrosion Resistance: Both 304 and 304L stainless steel offer excellent corrosion resistance in various environments, including atmospheric conditions and moderately corrosive environments. The corrosion resistance primarily comes from the high chromium content in these grades. The lower carbon content in 304L helps to minimize the formation of carbide precipitates, reducing the likelihood of sensitization and intergranular corrosion. Consequently, 304L stainless steel is often more resistant to intergranular corrosion in welded structures compared to 304 stainless steel.
Strength and Hardness: 304 and 304L stainless steel have similar strength and hardness properties. They both provide good strength and are capable of sustaining typical loads in various applications. The slight difference in carbon content does not significantly affect their mechanical properties.
What is the difference between 304 and 304L stainless steel in the application field?
Welding Applications: 304L stainless steel is particularly well-suited for welding applications due to its lower carbon content. The reduced carbon content minimizes the formation of chromium carbide precipitates at the grain boundaries during welding, which can lead to sensitization and subsequent intergranular corrosion. Therefore, 304L is commonly used in industries that require welding, such as the chemical, petrochemical, and pharmaceutical sectors. It allows for the fabrication of welded structures with enhanced resistance to intergranular corrosion.
Corrosive Environments: Both 304 and 304L stainless steel exhibit excellent corrosion resistance in various environments, including atmospheric conditions and moderately corrosive media. However, the lower carbon content in 304L provides added resistance to sensitization and intergranular corrosion. As a result, 304L is often preferred in applications where welded components are exposed to corrosive environments, as it helps mitigate the risk of corrosion along the weld zones.
Architectural Applications: In architectural applications, where aesthetics and corrosion resistance are vital, both 304 and 304L stainless steel are commonly utilized. However, the reduced risk of sensitization and intergranular corrosion makes 304L a preferred choice in environments where corrosion resistance is critical, such as coastal areas or highly polluted urban environments. In such settings, 304L stainless steel helps maintain the structural integrity and appearance of architectural components.
General-Purpose Applications: 304 stainless steel is widely used in various general-purpose applications. It is commonly found in food processing equipment, kitchen appliances, automotive parts, and structural components. Its versatility, corrosion resistance, and good mechanical properties make it suitable for a broad range of applications where welding is not a primary consideration.
The difference in cost-effectiveness between the two
In terms of cost-effectiveness, there is generally little difference between stainless steel 304 and 304L. Both grades are widely available and commonly used, so their prices tend to be comparable. The cost of stainless steel is influenced by various factors, including market conditions, availability, quantity, and specific requirements.
However, in certain cases, the cost of 304L stainless steel may be slightly higher than that of 304 stainless steel. This is because the production of 304L involves additional processing to reduce the carbon content. The extra steps in manufacturing can result in slightly higher production costs, which may be reflected in the price of 304L stainless steel products.
It’s important to note that the cost difference, if any, is typically minimal and may vary depending on the specific supplier or region. When considering the cost-effectiveness of stainless steel, it is crucial to assess the overall suitability of the material for the intended application, taking into account factors such as corrosion resistance, mechanical properties, and welding requirements.