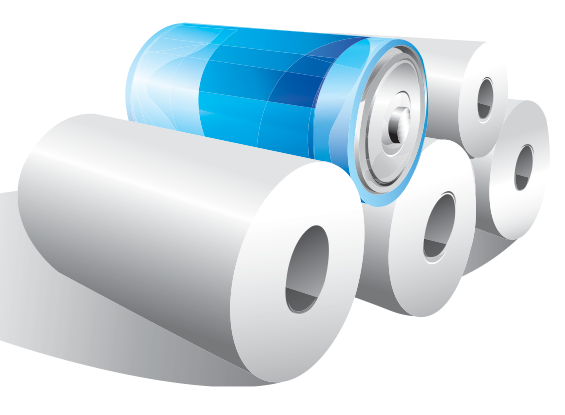

Battery case steel is a type of steel used to manufacture battery cases. This steel is known for its high strength and corrosion resistance. Battery case steel is also known for its ability to withstand high temperatures.
What is BDCK steel?
BDCK steel is a battery shell steel specially designed by Baosteel for punching alkaline or secondary battery shells. It is suitable for:
1) Battery case with high speed, deep drawing and thinning and stretching process
2) Battery case with strict appearance quality requirements
3) Battery cases with pre-nickel or post-nickel plating.
What are the main characteristics of BDCK steel?
1) Good stamping formability. It has the characteristics of deep drawing, thinning and small ear making.
2) High dimensional accuracy. Thickness accuracy of pockmarked battery case steel: +0.01mm2, slightly negative tolerance design of smooth battery case steel, to meet user stamping requirements: -0.007mm~0.003mm (suitable for thickness: 0.25~0.3mm).
3) High surface quality. The thickness accuracy of pockmarked battery steel: 0.25, 0.30, 0.50mm; the smooth battery steel is designed with a slight negative tolerance to meet the stamping requirements of users: 0.25, 0.30mm.
4) The characteristics of high-purity steel. Excellent intrinsic quality characteristics of materials can reduce the “trachoma defect” caused by the material; can reduce the “snowflake” defect caused by the material.
What are the mechanical properties of BDCK steel?
BDCK steel has high strength, excellent formability and good weldability, all important characteristics of a material used for battery casings. The following are the specific mechanical properties:
Thickness: 0.25-0.5, mm
Tensile strength: ≧275MPa
Elongation≧34%
Hardness: 40-56HRB
Add Your Heading Text Here
Battery case steel is made of carbon and iron combined to form a strong and durable metal that can withstand high temperatures and pressures. The manufacturing process begins by melting iron ore and coke in a blast furnace, which removes impurities from the iron and carbon. Molten steel is then poured into molds to form the desired shape. Once the steel has cooled and solidified, it can be used in batteries.
What is the punching process of BDCK steel?
The processing and forming of the steel case of the battery case is a key process in battery production. If the required deformation degree of the steel case exceeds the maximum deformation degree allowed by the material for one-time forming, the steel case cannot be stretched and formed at one time. Therefore, multiple drawing methods are generally used. method of stretching. Multi-stretch forming is to distribute the total deformation of the steel shell through multiple passes, and each stretch completes a part of the deformation, so that after multiple stretches, the steel shell is finally made. By controlling the die gap, it can be divided into two punching processes: equal thickness drawing and thinning drawing.
Can the battery case be punched with SPCC?
SPCC cold-rolled coils cannot be used to punch high-quality steel shells for batteries, because the cold-rolled coils with the brand name of SPCC are cold-rolled products for general purposes. Without targeted design for battery steel shells, many quality indicators cannot be met. The use of battery steel shells is required, so in order to ensure that the battery has a long-lasting and excellent performance during use. Please choose Baosteel BDCK special cold-rolled steel strip for battery steel case.
What are the benefits of using battery case steel?
When it comes to battery case steel, there are a number of advantages that make this material an attractive choice for a wide range of applications. Perhaps one of the most notable benefits is its high strength-to-weight ratio. This means that battery case steel is both strong and lightweight, making it ideal for use in a variety of environments. In addition, battery case steel is also resistant to corrosion and wear, meaning it can withstand repeated use without showing signs of wear. Finally, battery case steel is also recyclable, meaning it’s a sustainable option for those looking to reduce their environmental impact.
What are the advantages of BDCK battery case steel?
BDCK battery case steel has a high strength-to-weight ratio, making it ideal for a wide range of applications. However, there are some potential disadvantages to using this type of steel. Let’s take a closer look at the advantages and disadvantages of BDCK battery shell steel.
advantage:
– High strength-to-weight ratio: This makes BDCK battery case steel ideal for use in applications where weight is a factor, such as aircraft and automotive components.
– Good weldability and formability: BDCK battery case steel can be easily welded and formed into desired shapes, making it versatile and usable for various applications.
What are the disadvantages of BDCK battery case steel?
– Corrosion-prone: BDCK battery case steel is more prone to corrosion than other types of steel. This means it may not be the best choice for outdoor or marine applications.
– Not as heat resistant as other steels: BDCK battery case steel is not as heat resistant as other types of steel and should not be used in applications requiring high temperatures.
How to choose the BDCK battery shell steel that suits your needs?
There are a few things to consider when choosing the right type of steel for your BDCK battery case. The first is the thickness of the steel. The thicker the steel, the more durable it is. However, thicker steel is also more difficult to machine.
The second thing to consider is the type of finish on the steel. Coatings or platings help protect steel from corrosion and make it easier to clean. There are a variety of finishes to choose from, so you need to decide which one suits your needs.
In the end, you need to decide what price you are willing to pay for BDCK battery case steel. Steel prices vary widely, so it’s important to shop around and compare prices before buying.
Why choose So lucky BDCK steel?
Because So lucky BDCK steel is a tailor-made product for high-quality battery cases. Each process of product production is produced and managed according to special control standards.
What should be paid attention to when using BDCK steel?
1) Adjustment accuracy of equipment:
It mainly includes the adjustment of the transmission accuracy and the accuracy of the moving plane.
2) The adjustment accuracy of the mold:
According to the different punching materials, the mold needs to be adjusted precisely. Secondly, during the continuous stamping process, the parts of the mold will wear out. Once worn, the gap and angle will change slightly, which will affect the stamping.
The main objects of adjustment are: proportional distribution of stretching height, rounded corner adjustment of mold, gap adjustment, concave angle adjustment, and bottom chute adjustment.
3) The cooling system of the equipment:
The cooling flow rate and cooling effect have a very important cooling effect on the thermal expansion of the mold material. If the thermal expansion coefficient is large, the deformation of the mold will be large, which will cause large precision errors in each process, and it is easy to cause product defects or shutdown processing: thermal expansion coefficient The deformation of the small mold is small, the precision in each process is relatively stable, and there are fewer problems.
4) The lubrication system of the equipment:
Good lubrication of the mold can reduce problems such as surface wire drawing caused by friction during the punching and stretching process of the steel shell. During the stamping process, the lubricating oil for stamping should be replenished in time for the materials in the drawing process, and attention should be paid to the uniformity of the oil supply and the purity of the oil.
There are currently two oil supply methods for stamping lubrication: automatic oil supply for punch presses: atomization state and drop form.
The way of manual oiling: drip oil according to experience.
5) Cleaner production:
During the stamping process of the steel strip, avoid the adhesion of dust and other foreign matter to the steel strip, keep the environment of the stamping workshop clean, clean the mold regularly, and reduce defects such as wire drawing and punching caused by external media.